10.10.2022
Autofabriken als Inbegriff industrieller Effizienz
Auf den ersten Blick wirkt die moderne Automobilproduktion hochgradig effizient. Erst der genauere Blick offenbart das Potenzial zur Optimierung. Mithilfe von Quantencomputing will die Volkswagen AG dieses ausschöpfen und so langfristig Produktionszeiten verkürzen sowie die Verschwendung von Produktionsstoffen minimieren und somit Kosten sparen – also unmittelbaren Mehrwert schaffen.
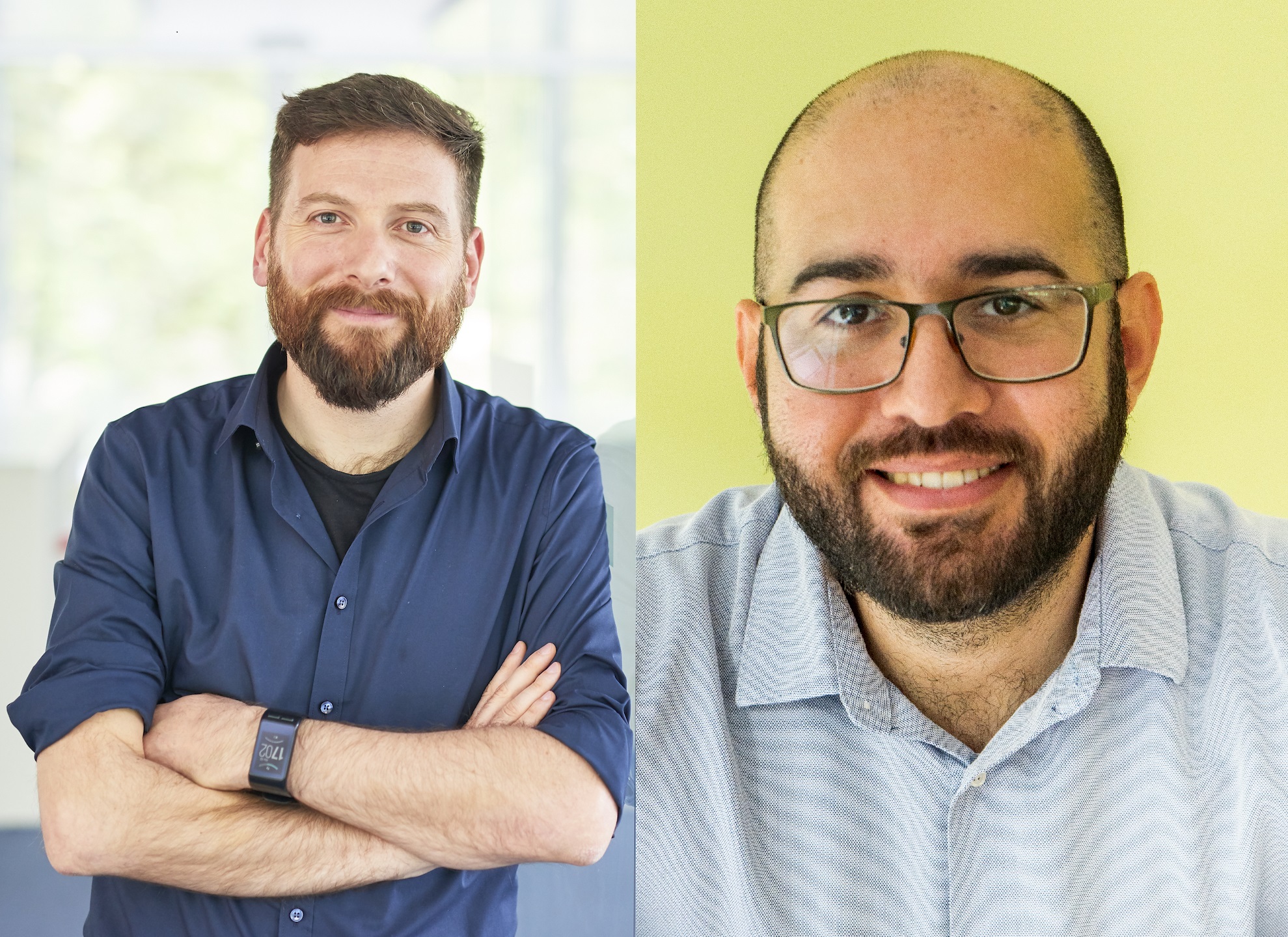
Gabriele Compostella, Quantum Computing Lead und Sheir Yarkoni, Quantencomputing-Experte bei der Volkswagen AG © Volkswagen AG
Ein neuer Blick auf die Effizienz in der Automobilproduktion
Autofabriken gelten oft als Inbegriff industrieller Effizienz. Ideal aufeinander abgestimmte Fließbänder und modernste Roboter, die unermüdlich und mit unfehlbarer Präzision immer wieder dieselbe Aufgabe wiederholen: Schwer vorstellbar, wie die Abläufe derartig optimierter Systeme noch weiter verbessert werden sollen. „Bis zu einem gewissen Grad funktionieren diese Systeme tatsächlich perfekt“, erklärt Dr. Gabriele Compostella, Quantum Computing Lead bei der Volkswagen AG. „Allerdings sind sie oft auch etwas starr und lassen sich nur schwer an veränderte Bedingungen anpassen. Kurzfristige Änderungen können aber jederzeit eintreten, etwa in den Schichtplänen der Arbeiter*innen, in der Logistik oder durch Verwerfungen wie die jüngste Chip-Shortage.“ Compostella glaubt, dass sich die Produktion von Automobilen weiter optimieren lässt.
Ein Beispiel ist die Lackierung von Karosserien. Jede Karosserie, die die Lackieranlage eines Werks erreicht, wird dort in zwei separaten Schritten lackiert: Zunächst wird eine Grundierung aufgetragen, die der Karosserie eine erste Lackschicht verleiht. Anschließend wird eine zweite Schicht, der sogenannte Basislack, aufgetragen. Dieser entspricht der von den Kunden in Auftrag gegebenen Farbe und bewegt sich im breiten Spektrum der vom Hersteller angebotenen Lackierungen. Die erste, darunter liegende Grundschicht kann dagegen in der Regel nur in zwei Farben auftreten: Weiß für hellere Farben des Basislacks sowie Schwarz für dunklere Farben. Soll die nächste Karosserie innerhalb der Produktionsreihenfolge eine andere Farbe erhalten, kann also ein Wechsel von einer hellen zu einer dunklen Grundierung (oder umgekehrt) stattfinden. Somit muss zunächst die entsprechende Grundierungsfarbe ausgetauscht werden. „In diesem Fall muss der Produktionsprozess angehalten werden, um die Maschine zu reinigen: Die Reste der alten Farbe werden ausgespritzt und die neue Farbe wird eingefüllt“, erklärt Compostella. „Eine einzelne Anpassung klingt zunächst vielleicht nicht besonders aufwändig, addiert man jedoch alle Anpassungen über einen oder mehrere Tage hinweg, belasten die dadurch insgesamt entstehenden Kosten die Produktion erheblich. Außerdem führt das Reinigen der Maschinen zwischen den Anpassungen zu einer Verschwendung von Grundierungslack, die es andernfalls nicht geben würde. Wenn man also die Gesamtzahl der Wechsel der Grundierungen minimiert, verringert man damit nicht nur den Energieverbrauch, sondern minimiert auch die Menge des während der Produktion entstehenden Abfalls und spart so letztlich Geld.“
Vom theoretischen Konzept zum Prototypen
Ginge es lediglich darum, die Reihenfolge zu ändern, in der die Karosserien in der Lackiererei ankommen, wäre die Minimierung der Grundierungswechsel trivial. „Doch so funktionieren Autofabriken in der Realität leider nicht“, so Sheir Yarkoni, der als Quantencomputing-Experte bei Volkswagen mit Compostella zusammenarbeitet. „Auf die Lackiererei folgt üblicherweise die Montage, wo Karosserieteile zu Karosserien zusammengesetzt werden. Aufgrund der vielen verschiedenen Modelle und Spezifikationen, die produziert werden, ist die Planung einer optimalen Reihenfolge der Automobile für die Montage ein komplexes Problem.“ Im Moment, so erklärt er, sei es besser, die Reihenfolge der Fahrzeuge, die in die Lackiererei kämen und sie wieder verließen, als Warteschlange mit feststehender Reihenfolge zu betrachten. Die Karosseriefarben, die in einer solchen Abfolge bestellt würden, seien jedoch nach wie vor zufällig verteilt. „Wir können uns also darauf konzentrieren, wie wir sie optimieren können.“ Die Frage aber, wie man diese Farbreihenfolge optimieren kann, bleibt mathematisch betrachtet hochkomplex. Oder, wie Yarkoni es ausdrückt: „Die angewandte Forschung zeigt, dass das Lackierproblem ein so genanntes ‚NP-schweres‘ Problem ist.“ Diese Art von Problem ist mit herkömmlichen Computern erwiesenermaßen schwer zu lösen, da seine Komplexität derart lange Bearbeitungszeiten erfordert, dass ihre Bearbeitung unmöglich oder zumindest sehr unpraktikabel erscheint.
Das hat Compostella, Yarkoni und ihr Team dazu veranlasst, das Problem als idealen Anwendungsfall des Quantencomputing zu betrachten. Der richtige Ansatz, wie sie heute wissen. „Zunächst konnten wir mit unserer Arbeit zeigen, auf welche Weise Quantencomputer dieses Problem besser lösen können als herkömmliche Rechner. Darauf aufbauend haben wir nicht nur einen Praxistest mit realen Daten auf echten Quantencomputern durchgeführt und veröffentlicht, sondern auch den Prototypen einer Softwareanwendung einschließlich eines Front Ends entwickelt. So etwas haben außer uns bislang nur sehr wenige getan“, bemerkt Yarkoni.
Early Adopters als Pioniere und Profiteure neuer Technologien
Noch hat Volkswagen seine Lösung nicht in die tägliche Produktion eingeführt. Compostella und Yarkoni lassen sich davon jedoch nicht beirren: „Es braucht natürlich Zeit, einen so neuartigen Ansatz in der Praxis zu implementieren“, sagt Compostella. Derzeit werden mehrere Umsetzungsmöglichkeiten diskutiert. „Es könnte sein, dass wir das System in einer unserer neuen Fabriken einsetzen. Oder wir arbeiten daran, es mit unserer zentralen Produktionsplanung zu verzahnen. Als Entwickler sind für uns beide Optionen spannend und attraktiv.“ Aus seiner Sicht war die Entwicklung des Use Case ohnehin bereits ein Erfolg: „Was wir gewonnen haben, sind vor allem Erfahrungen. Wir sind sehr stolz darauf, als erste in unserem Bereich den Weg von der theoretischen Analyse bis zu einer produktionsreifen Anwendung gemeistert zu haben.“ Gegenwärtig kämen Anwendungsfälle des Quantencomputing oft nicht über die theoretische Ebene hinaus, fügt er hinzu; sie blieben sozusagen im Labor stecken. „Aber es ist wichtig, dass wir uns daran gewöhnen, tatsächliche Anwendungen zu entwickeln, wenn auch nur in kleinem Maßstab und in Form von Prototypen. Nur so können wir unsere Ideen tatsächlich auf den Prüfstand stellen.“
Auch die Zusammenarbeit mit Kollegen aus anderen Unternehmen innerhalb von QUTAC habe Volkswagen viel gebracht, erklärt Sheir Yarkoni: „Viele haben in ihren Bereichen ähnliche Projekte durchgeführt, aber ihre Erfahrungen sind oft noch nicht verschriftlicht oder veröffentlicht, weil sie aus der täglichen Praxis stammen. Ohne QUTAC wären diese wertvollen Erkenntnisse für uns schwer zu reproduzieren oder sogar unzugänglich gewesen. Für alle Mitglieder ist es ein immenser Vorteil, sich innerhalb des Konsortiums austauschen zu können.“ Es sei eine Herausforderung, Probleme aus der realen Welt in praktikable mathematische Formulierungen zu verwandeln, sagt er. „Dazu braucht man eine Menge Wissen, Kreativität und Erfahrung. Man kommt nicht ans Ziel, wenn man sich den Dingen nur theoretisch nähert. Man muss mit Ideen experimentieren, sie ausprobieren und mit ihnen in der Praxis herumspielen. Vieles ist Trial and Error, und dabei lernen wir unschätzbare Dinge, die wir im nächsten Schritt anwenden können“, so Gabriele Compostella. „Jeden Schritt, den wir uns jetzt nach vorne wagen, sind wir unserer Konkurrenz später voraus.“